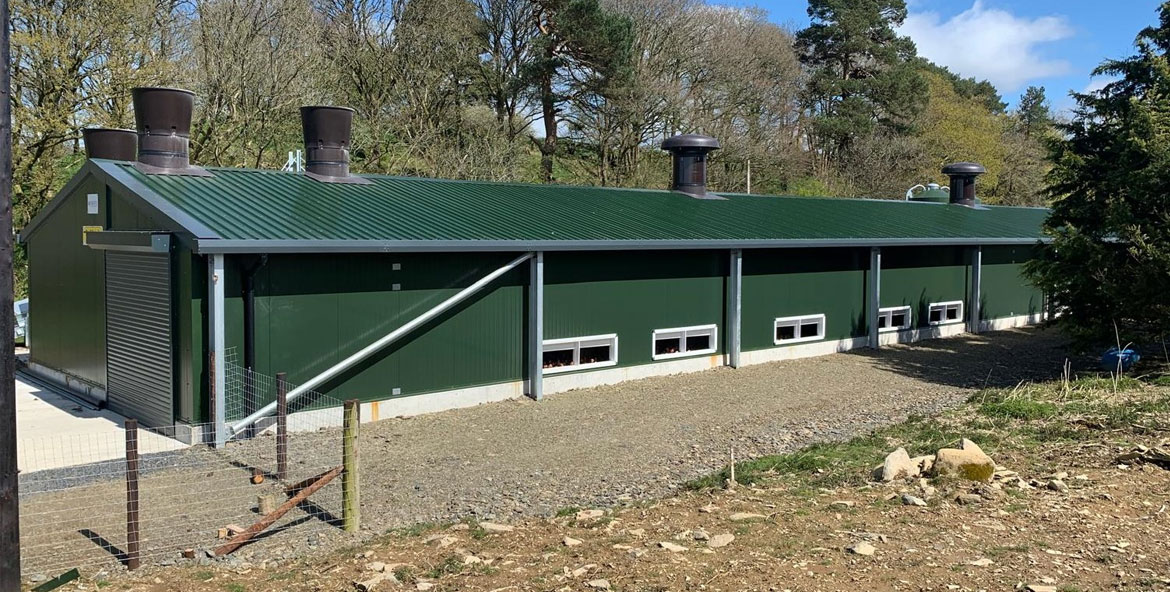
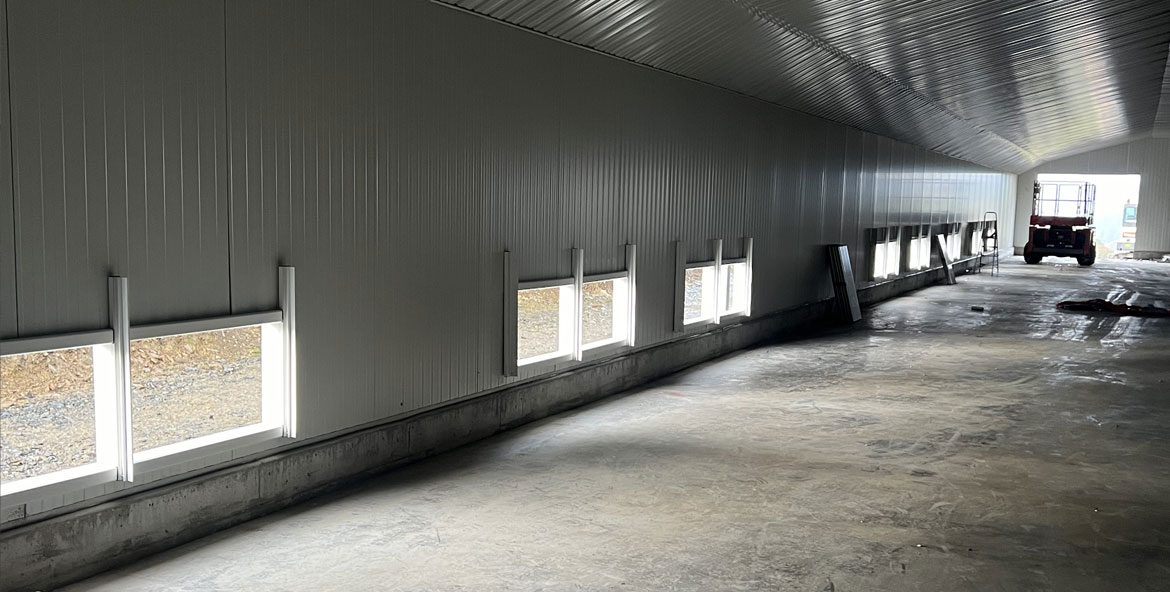
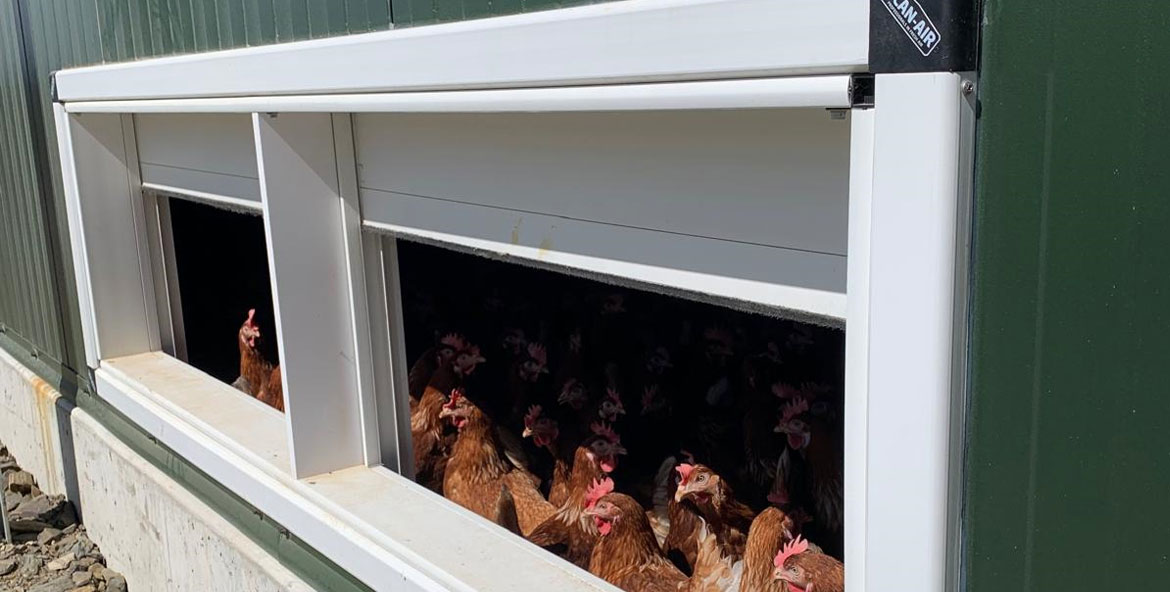
Brochure
Download our document to see specific data of the service and how we work.
Our One-Stop Build Solution
We recognise the intricate nature of managing multi-phase construction projects. That’s why we’ve developed a one-stop build solution that includes the design, planning and construction.
Do You Have a Project in Mind?
If you would like more information regarding our services, please get in touch. We will be happy to answer your questions.
Project Highlights:
Looking to replace an existing free-range unit that was worn out, the client had three goals: increase egg production, improve welfare standards, and be as energy-efficient as possible.
Knights came on board at an early stage and worked closely with the client to overcome the challenges of the build. The first challenge was the location, situated 1000ft atop an exposed hill, which meant we had to consider the best material suited to the environment. With limited space, we also carefully planned where to place the building while maximising its size to meet the client’s goals. Additionally, with a very tight turnaround time and hens already booked in, we had to consider the material to support the timeframes as well as the planned increased productivity on-site.
The Solution:
Our decided course of action was to build a traditional heavy sectional steel building but with a difference.
To combat time constraints and improve the energy efficiency of the building, we opted to use 80mm & 150mm composite panels for the side and gable elevations. This reduced the build time and greatly improved thermal retention.
All steel-framed buildings move by design. By using interconnecting composite panels, we almost eliminated the opportunity for any air gaps to develop, which usually occurs over time in traditional builds. This, in turn, improves internal temperatures, ventilation efficiency, and the welfare of the hens.
To address the client’s concerns about suitable double doors for the bird area access, considering the harsh weather conditions, we opted for a reinforced and braced composite roller shutter door. This provides the building with an excellent seal and robustness. For the pop-hole doors, we continued with the core goals of the client and opted for those offered by Scan-Air, which almost completely eliminate any air leaks when closed and do not allow any light into the building.
The result of this project has been positively received by the client and is an approach our teams are now rolling out on other builds.